- Out-of-Stock
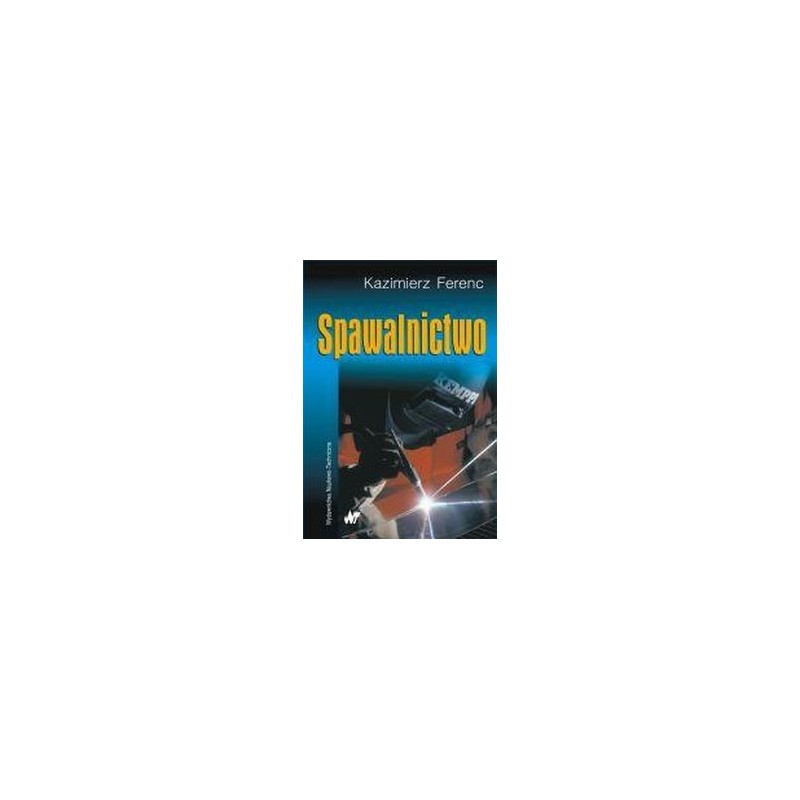
Table of Contents
1. WELDING CHEMICAL PROCESSES
2. CHARACTERISTICS OF WELDING PROCESSES
3. ADDITIONAL MATERIALS FOR WELDING
4. METALURGY OF WELDING PROCESSES
5. STRUCTURE OF WELDED JOINTS AND THEIR PROPERTIES
TECHNOLOGICAL
6. WELDING CONNECTIONS AND THEIR PROPERTIES
7. WELDING AND TECHNOLOGY OF WELDING METALS AND ALLOYS
8. WELDING PROCESSES
9. SOLDERING
10. WELDING APPLICATION PROCESSES
11. THERMAL CUTTING
12. QUALITY CONTROL IN WELDING
No product available!
Simon Monk
No product available!
No product available!
AVT kit for self-assembly of an adjustable symmetrical voltage supply. AVT1882 B
No product available!
TEST PLATE FOR BASCOM AVR COURSE MICROPROCESSOR COIL JOINT - A KIT FOR INDEPENDENT INSTALLATION
No product available!
No product available!
Radiator designed for use with the Odroid C1 minicomputer. It helps cool the quad-core processor in a short equipped Odroid C1.
No product available!
No product available!
No product available!
No product available!
No product available!
No product available!
32GB microSDHC Memory Card with SD Adapter, class 4, Kingston
No product available!
No product available!
No product available!
Graphic display, resolution 128x64 pixels, Type: COG, FSTN, 3.3V, NT7538 outline 67mm x 44mm
No product available!