- Out-of-Stock
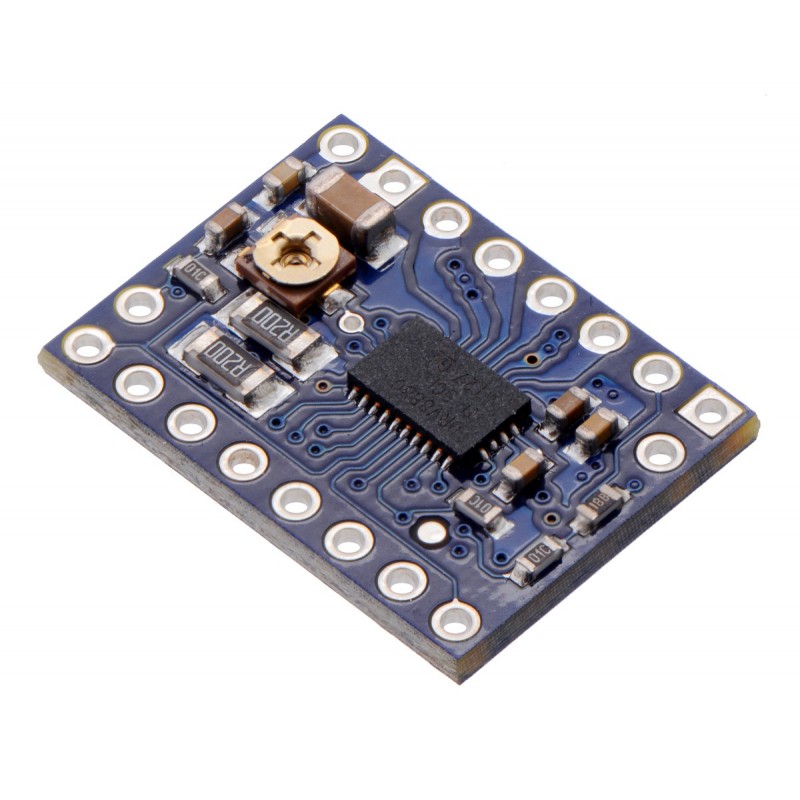
This product is a carrier board or breakout board for TI’s DRV8880 stepper motor drive. This stepper motor driver lets you control one bipolar stepper motor at up to 1.6 A output current per coil (see the Power Dissipation Considerations section below for more information). Here are some of the driver’s key features:
This product ships with all surface-mount components—including the DRV8880 driver IC—installed as shown in the product picture.
For alternative, pin-compatible stepper motor drivers, consider our DRV8825 carrier, DRV8834 carrier, or MP6500 carrier. The DRV8825 and MP6500 can deliver more current, and the DRV8834 operates down to 2.5 V, making it suitable for low-voltage applications.
Some unipolar stepper motors (e.g. those with six or eight leads) can be controlled by this driver as bipolar stepper motors. For more information, please see the frequently asked questions. Unipolar motors with five leads cannot be used with this driver.
The DRV8880 stepper motor driver carrier ships with one 1×18-pin breakaway 0.1" male header. The headers can be soldered in for use with solderless breadboards or 0.1" female connectors. You can also solder your motor leads and other connections directly to the board.
![]() |
Minimal wiring diagram for connecting a microcontroller to a DRV8880 stepper motor driver carrier (1/8-step mode). |
---|
The driver requires a motor supply voltage of 6.5 V to 45 V to be connected across VMOT and GND. This supply should have appropriate decoupling capacitors close to the board, and it should be capable of delivering the expected stepper motor current.
A 3.3 V output from the DRV8880’s internal regulator is made available on the V3P3 pin. This output can supply up to 10mA to external loads. When the driver is in sleep mode the 3.3 V output is disabled, so it cannot be used to pull up the sleep pin.
Warning: This carrier board uses low-ESR ceramic capacitors, which makes it susceptible to destructive LC voltage spikes, especially when using power leads longer than a few inches. Under the right conditions, these spikes can exceed the 50 V maximum voltage rating for the DRV8880 and permanently damage the board, even when the motor supply voltage is as low as 12 V. One way to protect the driver from such spikes is to put a large (at least 47 µF) electrolytic capacitor across motor power (VMOT) and ground somewhere close to the board.
Four, six, and eight-wire stepper motors can be driven by the DRV8880 if they are properly connected.
Warning: Connecting or disconnecting a stepper motor while the driver is powered can destroy the driver. (More generally, rewiring anything while it is powered is asking for trouble.)
Stepper motors typically have a step size specification (e.g. 1.8° or 200 steps per revolution), which applies to full steps. A microstepping driver such as the DRV8880 allows higher resolutions by allowing intermediate step locations, which are achieved by energizing the coils with intermediate current levels. For instance, driving a motor in quarter-step mode will give the 200-step-per-revolution motor 800 microsteps per revolution by using four different current levels.
The resolution (step size) selector inputs (M0 and M1) enable selection from the six step resolutions according to the table below. M0 is floating by default, while M1 has an on-board 10 kΩ pull-down resistor, so leaving these two microstep selection pins disconnected results in 1/8-step mode. For the microstep modes to function correctly, the current limit must be set low enough (see below) so that current limiting gets engaged. Otherwise, the intermediate current levels will not be correctly maintained, and the motor will skip microsteps.
M0 | M1 | Microstep Resolution |
---|---|---|
Low | Low | Full step |
High | Low | Non-circular half step |
Low | High | Half step |
High | High | 1/4 step |
Floating | Low | 1/8 step |
Floating | High | 1/16 step |
Each pulse to the STEP input corresponds to one microstep of the stepper motor in the direction selected by the DIR pin. These inputs are both pulled low by default through internal 100 kΩ pull-down resistors. If you just want rotation in a single direction, you can leave DIR disconnected.
The chip has two different inputs for controlling its power states: SLEEP and ENABLE. For details about these power states, see the datasheet. Please note that the driver pulls the SLEEP pin low through an internal 100 kΩ pull-down resistor, and the carrier board pulls the ENABLE pin high through an on-board 10 kΩ pull-up resistor. The default SLEEP state prevents the driver from operating; this pin must be high to enable the driver (it can be connected directly to a logic “high” voltage between 1.8 and 5.3 V, or it can be dynamically controlled by connecting it to a digital output of an MCU). The default state of the ENABLE pin is to enable the driver, so this pin can be left disconnected.
The DRV8880 also features a FAULT output that drives low whenever the H-bridge FETs are disabled as the result of over-current protection or thermal shutdown, or while the undervoltage lockout is disabling the chip. The carrier board connects this pin to the SLEEP pin through a 10k resistor that acts as a FAULT pull-up whenever SLEEP is externally held high, so no external pull-up is necessary on the FAULT pin. Note that the carrier includes a 1.5k protection resistor in series with the FAULT pin that makes it is safe to connect this pin directly to a logic voltage supply, as might happen if you use this board in a system designed for the pin-compatible A4988 carrier. In such a system, the 10k resistor between SLEEP and FAULT would then act as a pull-up for SLEEP, making the DRV8880 carrier more of a direct replacement for the A4988 in such systems (the A4988 has an internal pull-up on its SLEEPpin).
To keep faults from pulling down the SLEEP pin, any external pull-up resistor you add to the SLEEP pin input should not exceed 4.7k.
The current limit on the DRV8880 can be dynamically reduced using the current scaler pins (TRQ0 and TRQ1) as shown in the table below. These pins are controlled with digital high and low signals and can be used to scale the output current of the driver to 25%, 50%, 75%, or 100% of the current limit set by the VREF voltage. By default, the current scaler on the DRV8880 carrier is set to 100%. (Systems meant for the A4988 that connect the A4988’s SLEEP pin to RST will have a default scaler of 75%.)
TRQ0 | TRQ1 | Current scaler |
---|---|---|
High | High | 25% |
Low | High | 50% |
High | Low | 75% |
Low | Low | 100% |
The DRV8880 also allows the driver’s fixed off time to be configured using the TOFF pin. This is a tri-state pin that is floating by default, which results in a 10 μs default fixed off time. Bringing this pin low will change the fixed off time to 20 μs, and bringing it high will change the fixed off time to 30 μs. More details about the driver’s fixed off time can be found in the Current Regulation section of the DRV8880 datasheet.
By default, the DRV8880 carrier is configured to enable autotune. In this configuration, the decay mode is automatically selected each PWM cycle (slow, fast, or mixed decay), based on factors like the motor winding resistance and inductance and the motor’s dynamic speed and load. If a different decay mode is desired, the trace from the autotune pin (ATE) to V3P3 on the bottom of the board can be cut and the ATE pin on the corresponding surface-mount jumper (the one closer to the edge of the board) can be used to control the autotune state. Beside the jumper for ATE, there are also surface mount jumpers for the decay mode selection pins (D0 and D1). These pins are connected to ground by default, but if a decay mode that requires one or both pins to be floating or high is desired, the existing ground connections can be cut and a solder bridge can be used to connect the decay pins to the V3P3 pads above them. For more information on the different decay modes of the DRV8880, see its datasheet.
To achieve high step rates, the motor supply is typically higher than would be permissible without active current limiting. For instance, a typical stepper motor might have a maximum current rating of 1 A with a 5 Ω coil resistance, which would indicate a maximum motor supply of 5 V. Using such a motor with 9 V would allow higher step rates, but the current must actively be limited to under 1 A to prevent damage to the motor.
The DRV8880 supports such active current limiting, and the trimmer potentiometer on the board can be used to set the current limit. You will typically want to set the driver’s current limit to be at or below the current rating of your stepper motor. One way to set the current limit is to put the driver into full-step mode and to measure the current running through a single motor coil without clocking the STEP input. The measured current will be 0.7 times the current limit (since both coils are always on and limited to approximately 70% of the current limit setting in full-step mode).
Another way to set the current limit is to measure the voltage on the “ref” pin and to calculate the resulting current limit (the current sense resistors are 0.200 Ω). The ref pin voltage is accessible on a via that is circled on the bottom silkscreen of the circuit board. The current limit relates to the reference voltage as follows:
Current Limit = VREF * TRQ / 1.32
Where TRQ is the current scaling percent set by the TRQ0 and TRQ1 pins. So, for example, if you have a stepper motor rated for 1 A, you can set the current limit to 1 A by setting the reference voltage to about 1.32 V and leaving the current scaling pins (which are internally pulled down) disconnected.
Note: The coil current can be very different from the power supply current, so you should not use the current measured at the power supply to set the current limit. The appropriate place to put your current meter is in series with one of your stepper motor coils.
The DRV8880 driver IC has a maximum current rating of 2 A per coil, but the current sense resistors further limit the maximum current to 1.6 A, and the actual current you can deliver depends on how well you can keep the IC cool. The carrier’s printed circuit board is designed to draw heat out of the IC, but to supply more than approximately 1 A per coil, a heat sink or other cooling method is required.
This product can get hot enough to burn you long before the chip overheats. Take care when handling this product and other components connected to it.
Please note that measuring the current draw at the power supply will generally not provide an accurate measure of the coil current. Since the input voltage to the driver can be significantly higher than the coil voltage, the measured current on the power supply can be quite a bit lower than the coil current (the driver and coil basically act like a switching step-down power supply). Also, if the supply voltage is very high compared to what the motor needs to achieve the set current, the duty cycle will be very low, which also leads to significant differences between average and RMS currents. Additionally, please note that the coil current is a function of the set current limit, but it does not necessarily equal the current limit setting. The actual current through each coil changes with each microstep. See the DRV8880 datasheet for more information.
The DRV8880 carrier was designed to be as similar to our A4988 stepper motor driver carriers as possible, and it can be used as a drop-in replacement for the A4988 carrier in many applications because it shares the same size, pinout, and general control interface. There are a few differences between the two modules that should be noted, however:
In summary, the DRV8880 carrier is similar enough to our A4988 carriers that the minimum connection diagram for the A4988 is a valid alternate way to connect the DRV8880 to a microcontroller as well:
![]() |
Alternative minimal wiring diagram for connecting a microcontroller to a DRV8880 stepper motor driver carrier (1/8-step mode). |
---|
Size: | 0.6″ × 0.8″ |
---|---|
Weight: | 1.3 g1 |
Minimum operating voltage: | 6.5 V |
---|---|
Maximum operating voltage: | 45 V |
Continuous current per phase: | 1 A2 |
Maximum current per phase: | 1.6 A3 |
Minimum logic voltage: | 1.8 V4 |
Maximum logic voltage: | 5.3 V4 |
Microstep resolutions: | full, non-circular 1/2, 1/2, 1/4, 1/8, and 1/16 |
Reverse voltage protection?: | N |
PCB dev codes: | md32a |
---|---|
Other PCB markings: | 0J9581 |
Data sheet
Manufacturer BTC Korporacja sp. z o. o. Lwowska 5 05-120 Legionowo Poland sprzedaz@kamami.pl 22 767 36 20
Responsible person BTC Korporacja sp. z o. o. Lwowska 5 05-120 Legionowo Poland sprzedaz@kamami.pl 22 767 36 20
Bipolar stepper motor. It has a resolution of 200 steps/revolution (1.8° per step), a rated voltage of 10 V, and draws a current of 0.5 A per coil. Pololu 1208
Bipolar stepper motor. It has a resolution of 200 steps/revolution (1.8° per step), a rated voltage of 3.9 V, and draws a current of 0.6 A per coil. Pololu 1204
Bipolar stepper motor. It has a resolution of 200 steps/revolution (1.8° per step), rated voltage of 3.8 V, and has a current consumption of 0.67 A per coil. Pololu 1205
Bipolar stepper motor. It has a resolution of 200 steps/revolution (1.8° per step), a rated voltage of 4.5 V, and draws a current of 0.67 A per coil. Pololu 1206
No product available!
Bipolar stepper motor powered with a voltage of up to 12 V and a maximum current of 400 mA. SparkFun ROB-10551
Acrylic computer case for Orange Pi PC / PC Plus / PC 2, transparent. Orange Pi
No product available!
No product available!
UGEARS presents a new unique item for your collection of wooden models – loaded with fun, aimed at positive emotions, the Wolf-01 mechanical handgun.
This new arrival to UGEARS latest range is not a plain wooden toy where functionality is limited to imaginary shooting by means of yelling “Bang-bang!” The Wolf-01 is a proper mechanical handgun that can make up to 5 shots per round. It has outstanding performance and technical specifications, including the most important – a huge load of safe and peaceful fun! UGears 70047
No product available!
No product available!
No product available!
No product available!
No product available!
No product available!
No product available!
A set with a camera with a resolution of 1 MPx with an OV9281 sensor, a USB 3.0 adapter and a cable. ArduCAM EK024
No product available!
No product available!
The module enables the visual detection of the surface color, has a built-in RGB color sensor, photodiode KPS-5130. MOD-52
No product available!
AVT kit for self-assembly of a 4-channel digital thermometer. AVT3085 B
No product available!
No product available!
No product available!
No product available!
This breakout board for TI’s DRV8880 microstepping bipolar stepper motor driver features adjustable current limiting, overcurrent and overtemperature protection, and six microstep resolutions (down to 1/16-step).