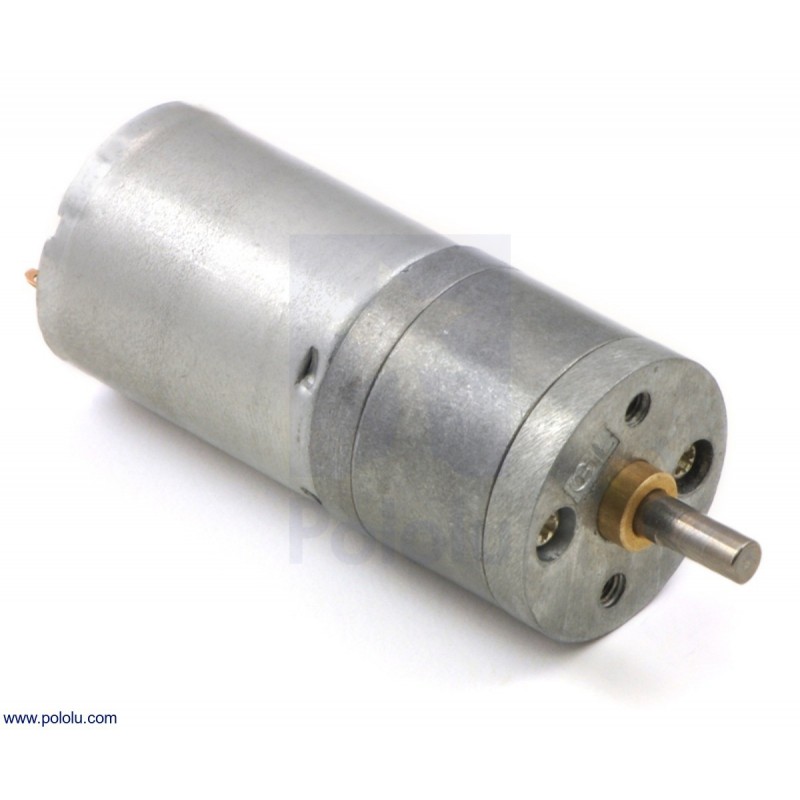
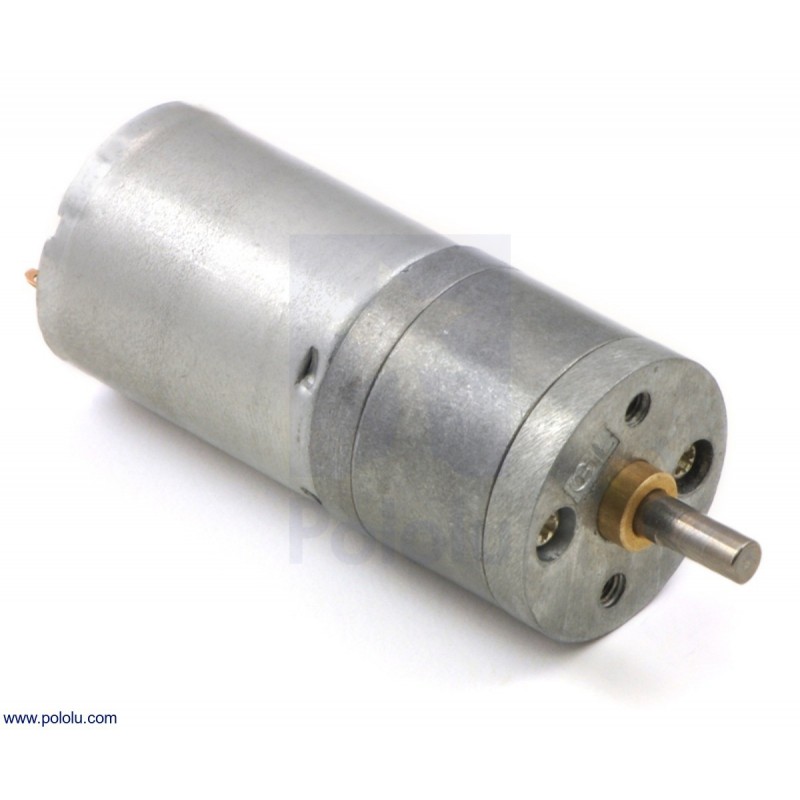
This gearmotor consists of a high-power, 12 V brushed DC motor combined with a 20,4:1 metal spur gearbox. The gearmotor is cylindrical, with a diameter just under 25 mm, and the D-shaped output shaft is 4 mm in diameter and extends 12.5 mm from the face plate of the gearbox.
Note!
Stalling or overloading gearmotors can greatly decrease their lifetimes and even result in immediate damage. For these gearboxes, the recommended upper limit for instantaneous torque is 15 kg-cm (200 oz-in); we strongly advise keeping applied loads well under this limit. Stalls can also result in rapid (potentially on the order of a second) thermal damage to the motor windings and brushes, especially for the versions that use high-power (HP) motors; a general recommendation for brushed DC motor operation is 25% or less of the stall current.Pololu 25D motors are available in two versions with the recommended voltage of 6 V and 12 V. These motors differ in power and current consumption. The power of LP motors in the 6 V and 12 V versions differs slightly, and the current consumed by the 12 V LP motors is more than half that of the 6 V LP motors. The power of the HP 12 V motors is noticeably greater than the HP 6 V, so the difference in the consumed current is not as big as in LP engines. It is possible to power the motors with a lower or higher voltage, but it is associated with lower power or a shorter life of the motors, respectively.
All motors have the same dimensions. Depending on the gear ratio, the gears differ in length, as shown in the technical drawing below. The metal gear housing has two tapped holes for M3 screws. The gearmotors weigh from 60 g to 110 g depending on the gear size.
![]() |
Dimensions of 25D motors in version with encoders (units in mm). |
---|
![]() |
Dimensions of 25D motors without encoders (units in mm). |
All Pololu 25D gearmotors are available in versions with a magnetic encoder and without an encoder. The encoder is mounted on an additional shaft on the opposite side of the main shaft. The shaft on which the encoder is mounted is led directly from the motor (without gear), which allows the installation of the encoder which works much more accurately than if it was mounted on the shaft behind the gear. The use of an encoder allows to determine the speed and position of the motor shaft and to apply these values in the PID controller feedback loop.
![]() |
![]() |
![]() |
Single-sided shaft motor | Motor with double-sided shaft and mounted encoder | A motor with a double-sided shaft, an encoder and a removed plastic cover |
A two-channel Hall effect encoder is used to sense the rotation of a magnetic disk on a rear protrusion of the motor shaft. The quadrature encoder provides a resolution of 48 counts per revolution of the motor shaft when counting both edges of both channels. To compute the counts per revolution of the gearbox output, multiply the gear ratio by 48. The motor/encoder has six color-coded, 8″ (20 cm) leads terminated by a 1×6 female header with a 0.1″ pitch, as shown in the main product picture. This header works with standard 0.1″ male headers and our male jumper and precrimped wires. If this header is not convenient for your application, you can pull the crimped wires out of the header or cut the header off. The following table describes the wire functions.
|
![]() |
||||||||||||||
Encoder A and B outputs for 25D mm HP 6V metal gearmotor with 48 CPR encoder (motor running at 6 V). |
The 4 mm diameter gearbox output shaft works with Pololu universal aluminum mounting hub for 4mm shafts, which can be used to mount our larger Pololu wheels (60mm-, 70mm-, 80mm-, and 90mm-diameter) or custom wheels and mechanisms to the gearmotor’s output shaft as shown in the left picture below. Alternatively, you could use our 4mm scooter wheel adapter to mount many common scooter, skateboard, and inline skate wheels to the gearmotor’s output shaft as shown in the right picture below.
![]() |
![]() |
![]() |
Black Pololu 80x10mm wheels | White Pololu 80x10mm wheels | Black Pololu 80x10mm wheel with motor mounted |
![]() |
|
|
Wild Thumper wheels Chrome | Wild Thumper wheels red matalic | Wild Thumper wheel with engine mounted |
![]() |
![]() |
|
Black scooter/skate wheels with 200 mm, 144 mm, 100 mm, 84 mm, and 70 mm diameters. | Aluminum Scooter Wheel Adapters |
The gearmotor face plate has two mounting holes threaded for M2.5 screws, and you can use our custom-designed 20D mm metal gearmotor bracket (shown in the left picture below) to mount the gearmotor to your project via these mounting holes and the screws that come with the bracket.
![]() |
![]() |
![]() |
Brackets for 25D engines | 25D engine with attached bracket and adapter | 25D engine mounted on a platform with a Scooter wheel |
We have a number of motor controllers and motor drivers that work with these 20D mm metal gearmotors. In particular, we recommend MC33296-based motor drivers, for which we have basic single and dual carriers and a dual-channel shield for Arduino.
![]() |
![]() |
![]() |
RoboClaw 2x7A Motor Controller (V5B) | Pololu Dual VNH5019 Motor Driver Shield for Arduino | Jrk G2 24v13 - DC motor controller |
We have an assortment of Hall effect-based current sensors to choose from for those who need to monitor motor current:
![]() |
![]() |
![]() |
Current sensor module (0-20A) with ACS712-20 | ACHS-7124 Current Sensor Carrier ±40A | Pololu 2452 - ACS711EX Current Sensor Carrier -15.5A to +15.5A |
Our offer includes motors with gear ratios from 4.4: 1 to 499: 1, with a rated voltage of 6 V and 12 V. All variants of motors with gears are available with and without a magnetic encoder. In addition, gearedless encoder motors are available to fit gears from the rest of the 25D motors.
Gear ratio | Type | Rated Voltage |
No-Load Speed | Stall Torque | No-Load Current |
Stall Current |
Single-Shaft | Dual-Shaft |
---|---|---|---|---|---|---|---|---|
1:1 | HP | 12 V | 10 200 RPM | 0.4 kg*cm | 0.3 A | 5.6 A | LINK | |
6 V | 10 000 RPM | 0.35 kg*cm | 0.275 A | 6.5 A | LINK | |||
MP | 12 V | 7 800 RPM | 0.2 kg*cm | 0.2 A | 2.1 A | LINK | ||
LP | 12V | 5 600 RPM | 0.15 kg*cm | 0.1 A | 1.1 A | LINK | ||
6 V | 6 200 RPM | 0.15 kg*cm | 0.25 A | 2.4 A | LINK | |||
4.4:1 | HP | 12 V | 2 250 RPM | 1.7 kg*cm | 0.3 A | 5.6 A | LINK | LINK |
6 V | 2 150 RPM | 1.5 kg*cm | 0.275 A | 6.5 A | LINK | LINK | ||
MP | 12 V | 1 700 RPM | 0.8 kg*cm | 0.2 A | 2.1 A | LINK | LINK | |
LP | 12 V | 1 200 RPM | 0.6 kg*cm | 0.1 A | 1.1 A | LINK | LINK | |
6 V | 1 300 RPM | 0.6 kg*cm | 0.25 A | 2.4 A | LINK | LINK | ||
9.7:1 | HP | 12 V | 1 030 RPM | 3.2 kg*cm | 0.3 A | 5.6 A | LINK | LINK |
6 V | 990 RPM | 2.8 kg*cm | 0.275 A | 6.5 A | LINK | LINK | ||
MP | 12 V | 1 030 RPM | 1.6 kg*cm | 0.2 A | 2.1 A | LINK | LINK | |
LP | 12 V | 560 RPM | 1 kg*cm | 0.1 A | 1.1 A | LINK | LINK | |
6 V | 590 RPM | 1.2 kg*cm | 0.25 A | 2.4 A | LINK | LINK | ||
20.4:1 | HP | 12 V | 500 RPM | 6 kg*cm | 0.3 A | 5.6 A | LINK | LINK |
6 V | 460 RPM | 5.5 kg*cm | 0.275 A | 6.5 A | LINK | LINK | ||
MP | 12 V | 370 RPM | 3 kg*cm | 0.2 A | 2.1 A | LINK | LINK | |
LP | 12 V | 260 RPM | 2 kg*cm | 0.1 A | 1.1 A | LINK | LINK | |
6 V | 290 RPM | 2.4 kg*cm | 0.25 A | 2.4 A | LINK | LINK | ||
34:1 | HP | 12 V | 290 RPM | 8.5 kg*cm | 0.3 A | 5.6 A | LINK | LINK |
6 V | 280 RPM | 6.5 kg*cm | 0.275 A | 6.5 A | LINK | LINK | ||
MP | 12 V | 220 RPM | 4.5 kg*cm | 0.2 A | 2.1 A | LINK | LINK | |
LP | 12 V | 150 RPM | 3 kg*cm | 0.1 A | 1.1 A | LINK | LINK | |
6 V | 170 RPM | 3.5 kg*cm | 0.25 A | 2.4 A | LINK | LINK | ||
47:1 | HP | 12 V | 210 RPM | 12 kg*cm | 0.3 A | 5.6 A | LINK | LINK |
6 V | 200 RPM | 8.5 kg*cm | 0.275 A | 6.5 A | LINK | LINK | ||
MP | 12 V | 160 RPM | 6 kg*cm | 0.2 A | 2.1 A | LINK | LINK | |
LP | 12 V | 110 RPM | 4.3 kg*cm | 0.1 A | 1.1 A | LINK | LINK | |
6 V | 120 RPM | 4.7 kg*cm | 0.25 A | 2.4 A | LINK | LINK | ||
75:1 | HP | 12 V | 130 RPM | 17 kg*cm | 0.3 A | 5.6 A | LINK | LINK |
6 V | 130 RPM | 11 kg*cm | 0.275 A | 6.5 A | LINK | LINK | ||
MP | 12 V | 100 RPM | 9 kg*cm | 0.2 A | 2.1 A | LINK | LINK | |
LP | 12 V | 71 RPM | 6 kg*cm | 0.1 A | 1.1 A | LINK | LINK | |
6 V | 78 RPM | 6.8 kg*cm | 0.25 A | 2.4 A | LINK | LINK | ||
99:1 | HP | 12 V | 100 RPM | 21 kg*cm | 0.3 A | 5.6 A | LINK | LINK |
6 V | 97 RPM | 15 kg*cm | 0.275 A | 6.5 A | LINK | LINK | ||
MP | 12 V | 76 RPM | 12 kg*cm | 0.2 A | 2.1 A | LINK | LINK | |
LP | 12 V | 55 RPM | 8 kg*cm | 0.1 A | 1.1 A | LINK | LINK | |
6 V | 58 RPM | 9.4 kg*cm | 0.25 A | 2.4 A | LINK | LINK | ||
172:1 | HP | 6 V | 56 RPM | 25 kg*cm | 0.275 A | 6.5 A | LINK | LINK |
MP | 12 V | 43 RPM | 18 kg*cm | 0.2 A | 2.1 A | LINK | LINK | |
LP | 12 V | 31 RPM | 13 kg*cm | 0.1 A | 1.1 A | LINK | LINK | |
6 V | 34 RPM | 14.5 kg*cm | 0.25 A | 2.4 A | LINK | LINK | ||
227:1 | MP | 12 V | 33 RPM | 23 kg*cm | 0.2 A | 2.1 A | LINK | LINK |
LP | 12 V | 23 RPM | 17 kg*cm | 0.1 A | 1.1 A | LINK | LINK | |
6 V | 25 RPM | 16 kg*cm | 0.25 A | 1.5 A | LINK | LINK | ||
378:1 | LP | 12 V | 14 RPM | 23 kg*cm | 0.1 A | 1.6 A | LINK | LINK |
6 V | 15 RPM | 22 kg*cm | 0.25 A | 1.1 A | LINK | LINK | ||
499:1 | LP | 6 V | 11 RPM | 30 kg*cm | 0.25 A | 2.4 A | LINK | LINK |
Data sheet
Manufacturer BTC Korporacja sp. z o. o. Lwowska 5 05-120 Legionowo Poland sprzedaz@kamami.pl 22 767 36 20
Responsible person BTC Korporacja sp. z o. o. Lwowska 5 05-120 Legionowo Poland sprzedaz@kamami.pl 22 767 36 20
Motor with 25 mm diameter and 54 mm length, 99:1 metal gear, 12 V operating voltage, 0,1 A to 1,1 A power consumption, 55 RPM speed and 8 maximum torque. Pololu 3255
No product available!
Motor with 25 mm diameter and 54 mm length, 99:1 metal gear, 6 V operating voltage, 0,55 A to 6,5 A power consumption, 97 RPM speed and 15 maximum torque. Pololu 1576
No product available!
Motor with 25 mm diameter and 52 mm length, 47:1 metal gear, 12 V operating voltage, 0,2 A to 2,1 A power consumption, 160 RPM speed and 6 maximum torque. Pololu 3229
No product available!
Motor with 25 mm diameter and 54 mm length, 75:1 metal gear, 12 V operating voltage, 0,1 A to 1,1 A power consumption, 71 RPM speed and 6 maximum torque. Pololu 3254
No product available!
Motor with 25 mm diameter and 73 mm length, 378:1 metal gear, 6 V operating voltage, 0,25 A to 2,4 A power consumption, 15 RPM speed, 22 maximum torque and 48 CPR encoder. Pololu 4830
No product available!
Motor with 25 mm diameter and 63 mm length, 9,7:1 metal gear, 6 V operating voltage, 0,55 A to 6,5 A power consumption, 990 RPM speed, 2,8 maximum torque and 48 CPR encoder. Pololu 4802
No product available!
Motor with 25 mm diameter and 67 mm length, 47:1 metal gear, 6 V operating voltage, 0,25 A to 2,4 A power consumption, 120 RPM speed, 4,7 maximum torque and 48 CPR encoder. Pololu 4825
No product available!
Motor with 25 mm diameter and 71 mm length, 227:1 metal gear, 6 V operating voltage, 0,25 A to 2,4 A power consumption, 25 RPM speed, 16 maximum torque and 48 CPR encoder. Pololu 4829
No product available!
Motor with 25 mm diameter and 69 mm length, 99:1 metal gear, 6 V operating voltage, 0,55 A to 6,5 A power consumption, 97 RPM speed, 15 maximum torque and 48 CPR encoder. Pololu 4807
Motor with 25 mm diameter and 71 mm length, 227:1 metal gear, 12 V operating voltage, 0,2 A to 2,1 A power consumption, 33 RPM speed, 23 maximum torque and 48 CPR encoder. Pololu 4869
No product available!
Motor with 25 mm diameter and 73 mm length, 499:1 metal gear, 6 V operating voltage, 0,25 A to 2,4 A power consumption, 11 RPM speed, 30 maximum torque and 48 CPR encoder. Pololu 4831
No product available!
Motor with 25 mm diameter and 69 mm length, 75:1 metal gear, 12 V operating voltage, 0,2 A to 2,1 A power consumption, 100 RPM speed, 9 maximum torque and 48 CPR encoder. Pololu 4866
No product available!
Motor with 25 mm diameter and 69 mm length, 99:1 metal gear, 6 V operating voltage, 0,25 A to 2,4 A power consumption, 58 RPM speed, 9,4 maximum torque and 48 CPR encoder. Pololu 4827
No product available!
Motor with 25 mm diameter and 52 mm length, 47:1 metal gear, 12 V operating voltage, 0,3 A to 5,6 A power consumption, 210 RPM speed and 12 maximum torque. Pololu 3205
No product available!
Motor with 25 mm diameter and 65 mm length, 20,4:1 metal gear, 12 V operating voltage, 0,1 A to 1,1 A power consumption, 260 RPM speed, 2 maximum torque and 48 CPR encoder. Pololu 4883
No product available!
Motor with 25 mm diameter and 50 mm length, 20,4:1 metal gear, 6 V operating voltage, 0,25 A to 2,4 A power consumption, 290 RPM speed and 2,4 maximum torque. Pololu 1583
No product available!
Motor with 25 mm diameter and 50 mm length, 20,4:1 metal gear, 12 V operating voltage, 0,3 A to 5,6 A power consumption, 500 RPM speed and 6 maximum torque. Pololu 3203